As Advanced Therapeutic Medicinal Products (ATMPs) surge in popularity and the market sees an increase in therapy development and available products, contemporary manufacturing processes must align with pertinent regulatory standards.
ATMPs are pharmaceutical products or drugs that necessitate modifying cellular products rather than simply transplanting them.
Adapting standard environmental monitoring technologies to suit ATMP production is feasible, and, when possible, integrating new technologies can strengthen the contamination control strategy for overall risk management in production environments and workflows.
The FDA and EMA are responsible for ensuring safety, effectiveness, and compliance with Good Manufacturing Practices in manufacturing. These GMP requirements include environmental monitoring in critical areas and consider the specific needs of ATMP production.
When more intricate cell therapy manufacturing is necessary, or when cells are utilized for treating different organs, the processes should adhere to distinct regulatory agency approvals to ensure production facilities present minimal risk (or acceptably low risk) to patients.
Overview of process
The preparation of typical ATMP products differs from traditional biopharma product manufacturing because it starts with cells initially obtained from the patient receiving treatment. These cells are gathered, modified according to the therapy, and then returned to the patient donor.
Since both the process and product are tailored to individual patients, ATMP batch sizes are small, and certain sterilization steps that could harm the final cellular product are not used. Consequently, the process flow must be kept aseptic to prevent the risk of contaminants and, importantly, to avoid cross-contamination between batches.
Gene therapy is somewhat different in that cells taken from one patient may be adjusted to suit a broader population of potential patients. Although batch sizes may be larger than those for individual cell therapy, they remain small compared to traditional pharmaceutical drug manufacturing.
These smaller batches are mostly handled manually throughout the process stages, which increases the potential for risks in the aseptic environment.
Transitioning to isolator glove boxes reduces the exposure to external contamination but can make certain manipulations more challenging. There is ongoing research into implementing robotics to shift the entire process to a 'single-box' manufacturing format, especially as production scales up.
Environmental monitoring
The primary aim of environmental monitoring in ATMP facilities is to demonstrate the highest level of control in two key areas:
- The aseptic manufacturing environment
- Minimizing the potential for cross-contamination between batches or manipulations
These two main processes can be categorized into Open processing and Closed processing.
In open system manufacturing, it is essential to maintain processes in a Grade A (ISO5) environment with unidirectional airflow, operating within a Grade B (ISO7) room environment.
These environments present the greatest risk of contamination from the surrounding environment because operators, who are the primary source of contamination, are close to the processing area, often reaching into the process to perform routine tasks.
Closed processing, on the other hand, effectively isolates the room environment from the processing environment. Manipulations are carried out through glove ports integrated within the isolator. Isolators also offer the possibility of automating CIP/SIP processing.
Environmental monitoring to demonstrate aseptic control
In seeking regulatory guidance for effective monitoring in aseptic manufacturing, the EU GMP Annex 1, which was recently updated and released in August 2022, provides specific information regarding the control of the aseptic environment, especially in Grade A critical areas.
It is crucial to conduct rigorous monitoring of the environment to ensure constant awareness of current conditions, including the detection of periodic events that could be catastrophic if overlooked. Continuous monitoring generates a steady flow of data, which can be used to identify trends.
Therefore, a comprehensive environmental monitoring program should be in place at the manufacturing facility. This program should cover non-viable airborne particles, viable airborne particulates, surface viable contamination, and personnel in the aseptic areas.
The program should define monitoring frequencies and sample locations, set warning and alarm limits for each area, and outline corrective actions in case of deviations from expected results.
If limits are exceeded, actions should include an investigation into the source of the issue, an assessment of its potential impact on the product, and measures to prevent a recurrence.
A Contamination Control Strategy (CCS) should incorporate the environmental monitoring program and be implemented facility-wide.
The CCS should define critical control points through risk assessment and assess the effectiveness of controls and monitoring measures for managing contamination risks. Monitoring techniques should be suitable for the needs identified in the Risk Assessment.
Grade A areas should have continuous monitoring (for particles ≥ 0.5 and ≥ 5 µm) at an appropriate sample flow rate (at least 28.3 LPM / 1 CFM) to capture all interventions, transient events, and system deterioration.
The system should frequently compare individual sample results with alert levels and action limits to promptly identify potential excursions. Alarms should be triggered if alert levels are exceeded, and procedures should specify actions to take in response to alarms, including considering additional microbial monitoring.
The requirement for continuous monitoring in Grade A areas can be met by using dedicated sensors at points of use. These sensors are connected to central monitoring software that can send alarms to cleanroom operators or messages to relevant groups.
These alert and alarm excursions are also permanently recorded in the audit trail of the system.
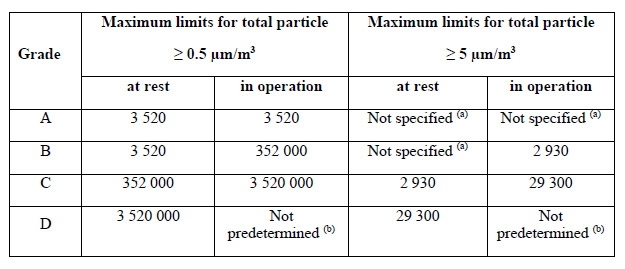
Figure 1. Annex 1 particle limits table. Source: Particle Measuring Systems
Risk assessment – Part 1
One aspect of the system concerns the selection of sample points, which should be determined based on a documented Environmental Monitoring Risk Assessment (EMRA). The EMRA should include the following information:
- Sampling locations
- Frequency of monitoring
- Monitoring method used
- Incubation conditions (e.g., time, temperature(s), aerobic and/or anaerobic conditions)
The risk assessment is based on inputs from the different groups within the facility.
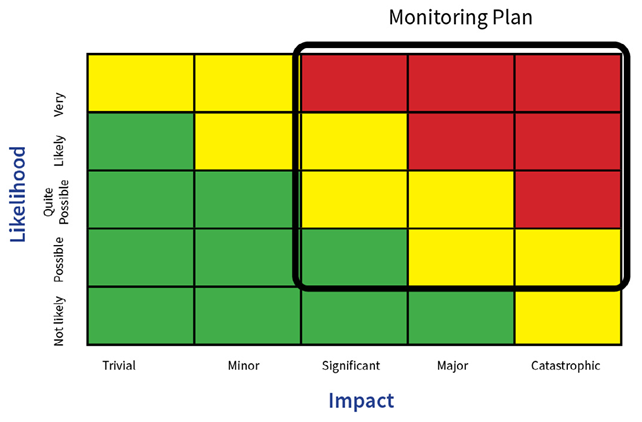
Figure 2. Monitoring plan. Image Credit: Particle Measuring Systems
Typical automated continuous monitoring system
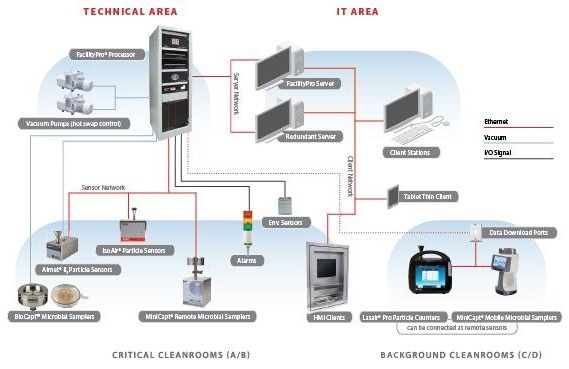
Figure 3. Schematic of theoretical facilitypro configuration. Image Credit: Particle Measuring Systems
The instrumentation used in constructing an integrated solution typically includes:
- Particle Counting – Continuous data necessitates a dedicated sensor at each location, continuously sampling during the setup and production phases of manufacturing. Sample points are installed within the hood or isolator line, connected to the sensor through a short length of sample tubing (no more than 2 meters, ideally shorter). The probe's location and orientation depend on the findings of the risk assessment.
- Microbial Sampling – When the risk assessment identifies the need for total particle counting, there is a corresponding requirement for microbial sampling.
- Active Air Sampling - In this method, only the sample head is placed within the environment, ensuring that any samples are not exhausted locally within the critical space. The sampling is quantitative and can run continuously for up to 4 hours*. Start and stop controls are managed through the software interface.
- Static/Passive Air Sampling – Here, a plate is positioned in the local environment for up to 4 hours, providing valuable data for understanding the microbial risk. While impaction sampling can harm certain microbiology, and it may not be part of routine monitoring, it should be included in qualification studies and the EMPQ.
- Rapid Automated Microbial Monitoring (RMM) – The use of autofluorescence microbial instrumentation, capable of distinguishing between inert and biological particles in real-time, introduces a new dimension in demonstrating environmental control. Alongside total particle counting and active and passive air sampling, it contributes to making quick decisions when an area's control is compromised.
It is important to note that demonstrating asepsis and sterility is not guaranteed by a single piece of evidence alone. This information serves as the introduction to the environmental monitoring chapter in EU GMP Annex 1.
9 Environmental & Process Monitoring
9.1 The environmental and process monitoring program at the site is an integral component of the overall CCS. It serves the purpose of overseeing the controls implemented to reduce the risk of both microbial and particle contamination. It is crucial to recognize that the reliability of each monitoring system's elements (viable, non-viable, and APS) is limited when assessed independently and should not be considered as standalone indicators of asepsis. When viewed collectively, the results contribute to confirming the reliability of the system's design, validation, and operation that they are monitoring.
The accumulation of data and information is what provides a comprehensive understanding of the effectiveness of the environmental controls implemented.
The correlation between particle and microbial data has been the established foundation for demonstrating environmental control for more than two decades, with the ideal goal of having no particles ≥ 5 µm.
This approach emerged from the belief that larger particles could potentially carry microbiological agents or be clusters of microbiological entities capable of remaining viable in the dry air commonly found in cleanroom environments.
Once traditional microbiology and RMM confirm the presence of particles detected through particle counting, the intersection of these three data sets helps to identify where particles ≥ 5 µm may be potentially harmful, both microbiologically and in real-time.
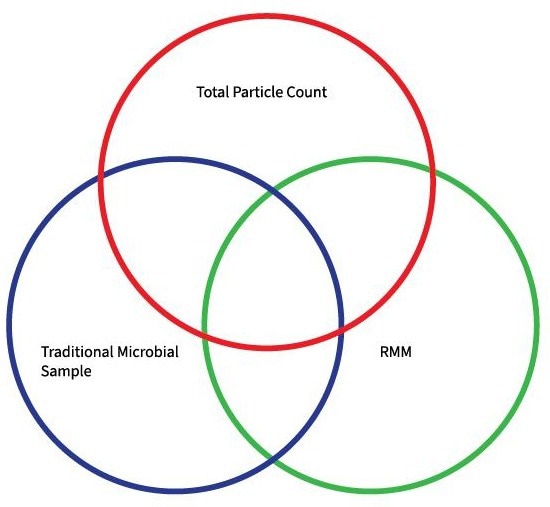
Image Credit: Particle Measuring Systems
Environmental monitoring to demonstrate cross-contamination control
The ability of a program to demonstrate resistance to cross-batch contamination or intra-batch contamination depends on the type of processing involved. Many facilities employ individual rooms for each batch, where a single cleanroom is dedicated to the processing stages and filling of one product batch.
In each of these rooms, there is a central bio-safety hood within a Grade B background. Operators within each space are responsible for tasks such as preparation, gowning, cleaning, and environmental monitoring.
The location of sample points may need to consider the various activities within the hood or room, requiring flexibility in the design of the monitoring system. Once a process is completed, the room is then prepared for the next batch of products.
Environmental monitoring is conducted at the start and end of each batch to demonstrate separation and assess the effectiveness of cleaning and sanitization procedures. A continuous monitoring system uses tags in the data to isolate each batch record without the need to halt monitoring.
This enables smooth transitions between different process phases, with distinct alert and action limits assigned to each phase's activities.
In cleanroom operations where a production line process is established (i.e., one product manipulation is performed at each stage and then moves forward along the process for subsequent steps), the environmental sample probe's location can be better aligned with the process.
Each step can be continuously monitored, and unique data identifiers can be added via barcodes during the 'at rest' phases between batches. A final report summarizing progress and rest phases can be generated at the end of processing.
When processing occurs within different modules of an isolator, it is possible to sanitize between batches when required. Alternatively, sanitization and surface monitoring can be conducted to demonstrate compliance.
For Quality by Design (QbD) operations, the process can be validated, and data tags can indicate that specific functions within batches occurred, reducing reliance on finished product testing compared to past practices.
There is also a third hybrid operation, where functions are divided between lower-grade zones and those requiring unidirectional flow. In such cases, data tracking becomes essential for reporting.
Batch identification tags within the data, such as barcodes or RFID, facilitate easier reporting of the finished product. Intra-batch isolation primarily focuses on critical risk activities, and monitoring remains continuous throughout the process.
Environmental data reporting
Data and Status Information Displays – Since the collected data is now multivariate, a central reporting tool can be applied. This tool integrates data from various environmental components and includes tagging for product tracking throughout production.
It enables us to visualize the facility layout with dashboards showing current data and status information for each batch in relation to the room and stage it is in. Additionally, data, status, and sampling information can be viewed for each dedicated area on a single screen.
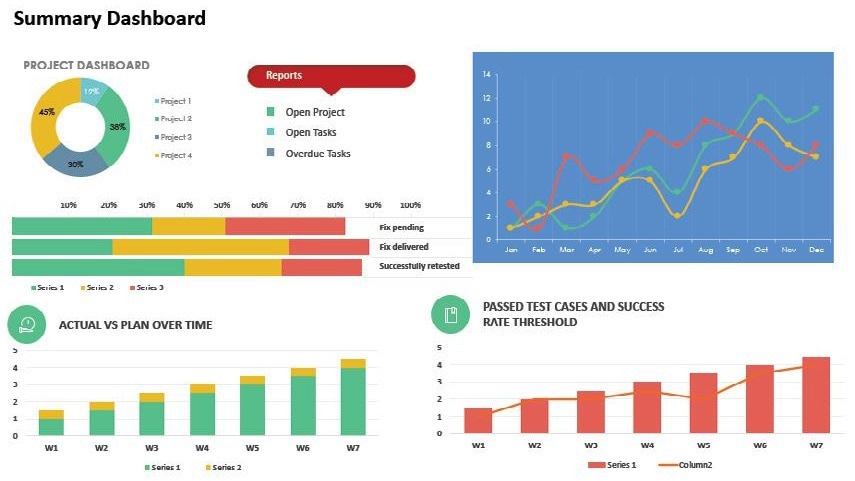
Image Credit: Particle Measuring Systems
Report Generator - The software includes a report generator capable of producing human-readable reports for all recorded data. These reports cover audit trails (events), data/statistical summaries, and trend charts.
The system should have the ability to retrieve historical data as defined in the site User Requirement Specification for the associated system. Using filters for data, time, location, and batch, data should be easily accessed and, when necessary, exported or printed to support product release.
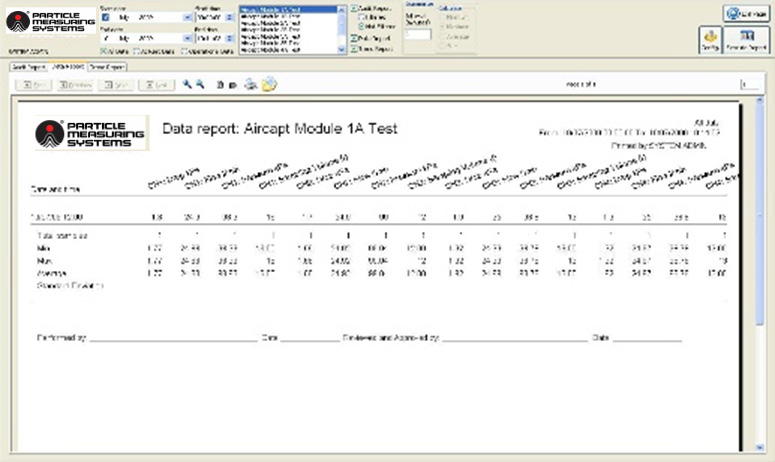
Image Credit: Particle Measuring Systems
Alarms - Appropriate alarms based on the product and process steps are established, and these alarms can be tracked and reported through the dashboard interface. The display includes an alarm acknowledgment function and provides details like date, time, area, description, and other alarm information. It also offers the capability to sort alarms using various criteria.
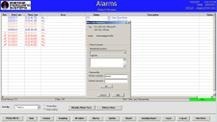
Image Credit: Particle Measuring Systems
Alarms based on trends should involve a review of the process to identify any increasing excursions from action limits or alert levels. The identification of consecutive or frequent excursions from alert levels may suggest a common cause.
For microbial limits, it is crucial to consider not only the quantity of CFU detected but also any changes in qualitative information, such as the type and predominance of specific organisms.
Risk assessment – Part 2
The information collected during environmental data processing should inform production activities. Operations should be reviewed when specific functions raise environmental concerns, such as when baseline values increase toward alert or actionable thresholds.
The review should involve a gap analysis between the initial risk assessment and a review of control points, any associated changes for improvement, or enhanced/additional monitoring to ensure coverage of potential functions that might cause future defects.
Summary
A continuous monitoring system for environmental parameters, including total particles, traditional microbiology, rapid microbiology, air velocity, temperature, humidity, and air exchange rates, will demonstrate the required maintenance of the cleanroom.
Associating the data with the batch also allows us to demonstrate the establishment and maintenance of intra-batch separation, and records of sanitization can be added to complete the batch record. All this data can be visualized on a central dashboard, enabling fast and accurate analysis.
Acknowledgments
Produced from materials originally authored by Mark Hallworth from Particle Measuring Systems.
About Particle Measuring Systems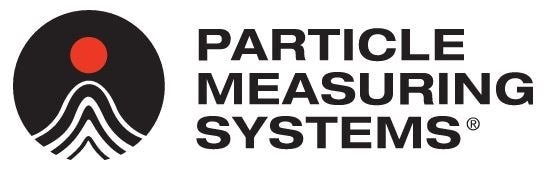
Particle Measuring Systems has 35 years experience designing, manufacturing, and servicing microcontamination monitoring instrumentation and software used for detecting particles in air, liquid, and gas stream as well as molecular contamination monitoring.
Specific applications include cleanroom monitoring, parenteral sampling, filter and in-line testing in deionized water and process chemicals, and point-of-use monitoring of inert gases and in-situ particle monitoring. Specialty monitoring includes parts cleanliness testing with a highly automated solution.
Particle measuring systems
Whether you want to protect product or meet industry requirements, such as ISO 14644, USP 797, or GMP, Particle Measuring Systems has a large variety of particle counters and molecular monitors to meet your needs. With 35 years experience, we have the proven reliability to support your application.
Particle counters
Protect your product with our reliable particle counters. We have airborne, portable, and liquid particle counters for a wide variety of applications including DI water, chemicals, and cleanroom monitoring. Compare particle counters or learn how to monitor your cleanroom or product by reading our papers.
Molecular contamination monitors
Molecular contamination creates costly problems to high value products, production processes, and equipment surfaces. We have solutions for both Airborne Molecular contamination (AMC) and Surface Molecular contamination (SMC). With parts-per-trillion limits of detection, real-time sampling, NIST traceable calibrations, and various data analysis packages, you can monitor in confidence.
Gas detectors
If you need gas detectors for process control or continuous emissions monitoring, we can help. Get real-time, reliable results with our ammonia, hydrogen fluoride, and chlorine detectors for worker protections, CEMs, and pollution monitoring.
Sponsored Content Policy: News-Medical.net publishes articles and related content that may be derived from sources where we have existing commercial relationships, provided such content adds value to the core editorial ethos of News-Medical.Net which is to educate and inform site visitors interested in medical research, science, medical devices and treatments.