Despite their frequent interchangeable use, understanding the distinction between validation and qualification is critical in pharmaceutical environments. Validation is a broader concept encompassing qualification, both adhering to good practice principles to ensure intended outcomes are met.
Qualification is a key documented process tailored for each pharmaceutical process. It involves designing equipment to achieve expected efficiency and performance while complying with technical regulations. This process includes a comprehensive assessment of the equipment’s suitability for its intended use, aligning with Annex 15 requirements.
Image Credit: Particle Measuring Systems
On the other hand, validation is the assurance that procedures, equipment, materials, or systems consistently produce desired results. Qualification underpins this by providing documented evidence of a system or process functioning as intended.
Successful execution of these processes demands a coordinated plan involving engineering, maintenance, quality control (QC), and quality assurance (QA) departments. Appointing a project leader centralizes information and streamlines phases.
Employing tools like Gantt charts enhances project management, ensuring engineering activities align with quality requirements. This is managed by QA through change control processes.
QC's role in validation and environmental classification is vital for data collection, emphasizing the need for an integrated approach. Staff training in skills and knowledge is crucial for efficiently achieving objectives and equipping them to tackle work-related challenges.
Recent updates to Annex 1, affecting smoke study and freeze-drying processes, necessitate synchronization across departments. Moksad has become integral in qualifying filling lines and in assessing risks in aseptic techniques for contamination control. Regular reviews of these studies guide best practices and training for sterile environment work.
Smoke studies play a crucial role in shaping the monitoring plan and defining parameters for risk assessment when determining sampling points.
As for the utilization, Annex 1 grants pharmaceutical companies an extra year to align with other document points. It has become evident that moving towards automated systems is necessary, where loading and unloading tasks are no longer performed directly by operators but rather with the use of barrier systems.
The stability of the localizer should also be carefully assessed within the Cleanroom Classification System (CCS), necessitating validation and testing of the holding time between the salutation cycle and effective use during the acceptance process.
The frequency of lyophilizer salivation must also be determined based on the system design and within the CCS. In situations with high associated risks, civilization is required for each batch.
Another crucial aspect involves preserving the Lifelizer’s integrity, necessitating validation and periodic testing of the filter used for integrity maintenance with each batch.
When considering an online total particle counter, one naturally envisions a system composed of multiple probes. These probes should be configured with sampling recipes and subjected to a risk assessment to determine work volume and sampling frequency.
For online total particle counters, configuring probes with sampling recipes and conducting a risk assessment to determine work volume and frequency is the first step. This is followed by process mapping, PK performance qualification protocol development, and system validation.
After completing qualification phases, system management, represented by ASP, will be implemented, leading to established alarm and action limits based on significant data collection. At this juncture, the process flow can be considered complete.
Requalification, applicable to both clean rooms and personnel, is also mandated as per Annex 1. Grade B areas require biannual requalification, while grades C and D need annual requalification. Personnel requalification is necessary following disqualification, including participation in aseptic processing simulations and UPS.
When validating various processes, such as sterilization and acceptance process simulation or disinfectants, the frequency typically depends on the specific topic. It is thus advisable to determine the frequency using a quality risk management tool.
About Particle Measuring Systems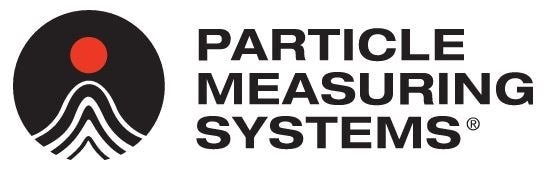
Particle Measuring Systems has 35 years experience designing, manufacturing, and servicing microcontamination monitoring instrumentation and software used for detecting particles in air, liquid, and gas stream as well as molecular contamination monitoring.
Specific applications include cleanroom monitoring, parenteral sampling, filter and in-line testing in deionized water and process chemicals, and point-of-use monitoring of inert gases and in-situ particle monitoring. Specialty monitoring includes parts cleanliness testing with a highly automated solution.
Particle measuring systems
Whether you want to protect product or meet industry requirements, such as ISO 14644, USP 797, or GMP, Particle Measuring Systems has a large variety of particle counters and molecular monitors to meet your needs. With 35 years experience, we have the proven reliability to support your application.
Particle counters
Protect your product with our reliable particle counters. We have airborne, portable, and liquid particle counters for a wide variety of applications including DI water, chemicals, and cleanroom monitoring. Compare particle counters or learn how to monitor your cleanroom or product by reading our papers.
Molecular contamination monitors
Molecular contamination creates costly problems to high value products, production processes, and equipment surfaces. We have solutions for both Airborne Molecular contamination (AMC) and Surface Molecular contamination (SMC). With parts-per-trillion limits of detection, real-time sampling, NIST traceable calibrations, and various data analysis packages, you can monitor in confidence.
Gas detectors
If you need gas detectors for process control or continuous emissions monitoring, we can help. Get real-time, reliable results with our ammonia, hydrogen fluoride, and chlorine detectors for worker protections, CEMs, and pollution monitoring.
Sponsored Content Policy: News-Medical.net publishes articles and related content that may be derived from sources where we have existing commercial relationships, provided such content adds value to the core editorial ethos of News-Medical.Net which is to educate and inform site visitors interested in medical research, science, medical devices and treatments.