Henniker's advanced plasma surface treatment systems feature large format vacuum chambers and several cutting-edge features, all with the dependability of recipe-driven PLC control.
They are configurable tools that are strong enough for trustworthy and repeatable industrial processing and concurrently flexible enough to research and develop leading-edge plasma processes.
The NEBULA range has been developed around the core technologies in plasma process development and surface treatment.
With chamber volumes varying from 50 L to 150 L, every instrument is configured with several parts tray/electrodes for vertical or horizontal mounting arrangements. One option for processing a large volume of small parts is to opt for a high-capacity rotary drum mechanism, for example.
NEBULA plasma systems are employed for cleaning, enhancing adhesion, and improving surface wetting through plasma surface activation. These treatments can be performed uniformly on a range of materials, including polymers, metals, composites, ceramics, and glass.
Every NEBULA system comes with a distinctive feature - an optional monomer dosing inlet. This fully automated device enables the introduction of a broad spectrum of liquid monomers for producing permanently functionalized surfaces through plasma polymerization. This significantly extends the range of plasma surface treatment possibilities in a single machine.
Benefits
- Standalone unit
- Easy-to-use recipe-driven interface
- Limitless recipes and steps for every recipe
- Liquid dosing inlet option
- Quick treatment time
- Accurate and repeatable
- No risky emissions
Features
- Chamber volumes range from 50 L to 150 L
- Horizontal, vertical, and rotary
- Plasma polymerization inlet
- PLC control
- Drum parts tray options available
- Completely automated and recipe-driven processes
Models
NEBULA plasma surface treatment systems feature huge format vacuum chambers and several advanced features, all with the reliability of recipe-driven PLC control.
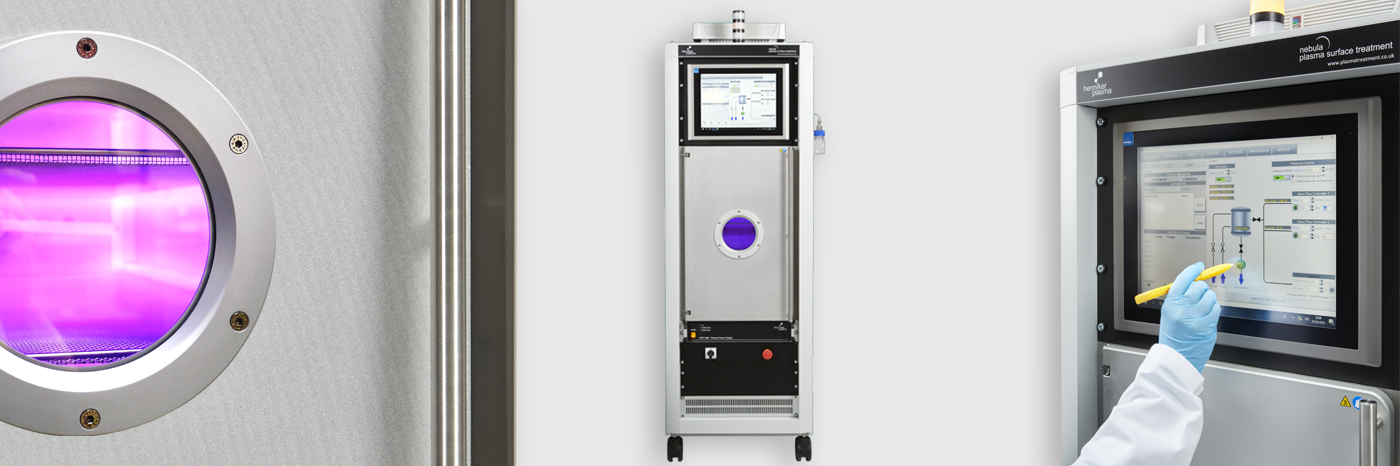
Image Credit: Henniker Plasma