In this interview, Michael Nilsson, the Assistant Director of Liquid Handling at FORMULATRIX , talks to News Medical about simplifying assay development and optimization and the different instruments that can be used to minimize cost.
I am curious about the cost of your chips for the Mantis. Given that you've talked about saving money on pipette tips and reducing plastic waste, does this mean we'd be spending more on these chips instead?
Great question! A pack of six Mantis chips is priced at around $600, meaning each one is around $100 dollars each. That might seem like a lot, but each of these chips can last up to 1 million diaphragm cycles if they're well-maintained and cleaned. You can wash and reuse these chips multiple times, so depending on how frequently you use them, a single chip could last several months under high use if you take good care of it.
At what threshold does the Mantis become beneficial for DoE? Our lab isn't really high-throughput as of now; we're still manually preparing our plates. At what plate count, daily or weekly, does it make sense for us to consider using Mantis?
Good question. Even for labs with lower throughput, the Mantis can be a game-changer, especially when it comes to DoE. The system can greatly streamline the process due to the intricate nature of some of these experimental designs. To give you an idea, if you're handling even just 2-3 plates a day, you'll find the Mantis to be a valuable addition to your lab, both in terms of time and cost savings.
Is it possible for the TEMPEST to dispense varying volumes of up to 8 different reagents into 384 assay plates all at once?
Absolutely! Given the right configuration, a Tempest system with 8 chips and the independent control module can dispense variable volumes of 8 different reagents into a 96 wells of a 384-well assay plate simultaneously. If you have any specific workflow or require deeper technical insight, please don't hesitate to get in touch with us. We are here to help you out.
What is the battery timing for the ROVER, and how often do we need to charge them? Does my experiment stop there if I'm moving plates between systems and the battery runs low? Also, if a ROVER is stuck somewhere, it results in a traffic jam and affects my other experiments as well?
Good rover questions! So, our fleet manager software, which manages the ROVER network, is pretty robust in handling these complexities. When you instruct it to move a plate from System A to System B, it will automatically determine which ROVER is nearest to the task and which one has the most battery left. If any Rover battery is getting low, it will schedule the ROVER to a charging dock. Plus, the integrated computer vision technology ensures smooth, collision-free navigation. So, you can be rest assured your experiments will run smoothly.
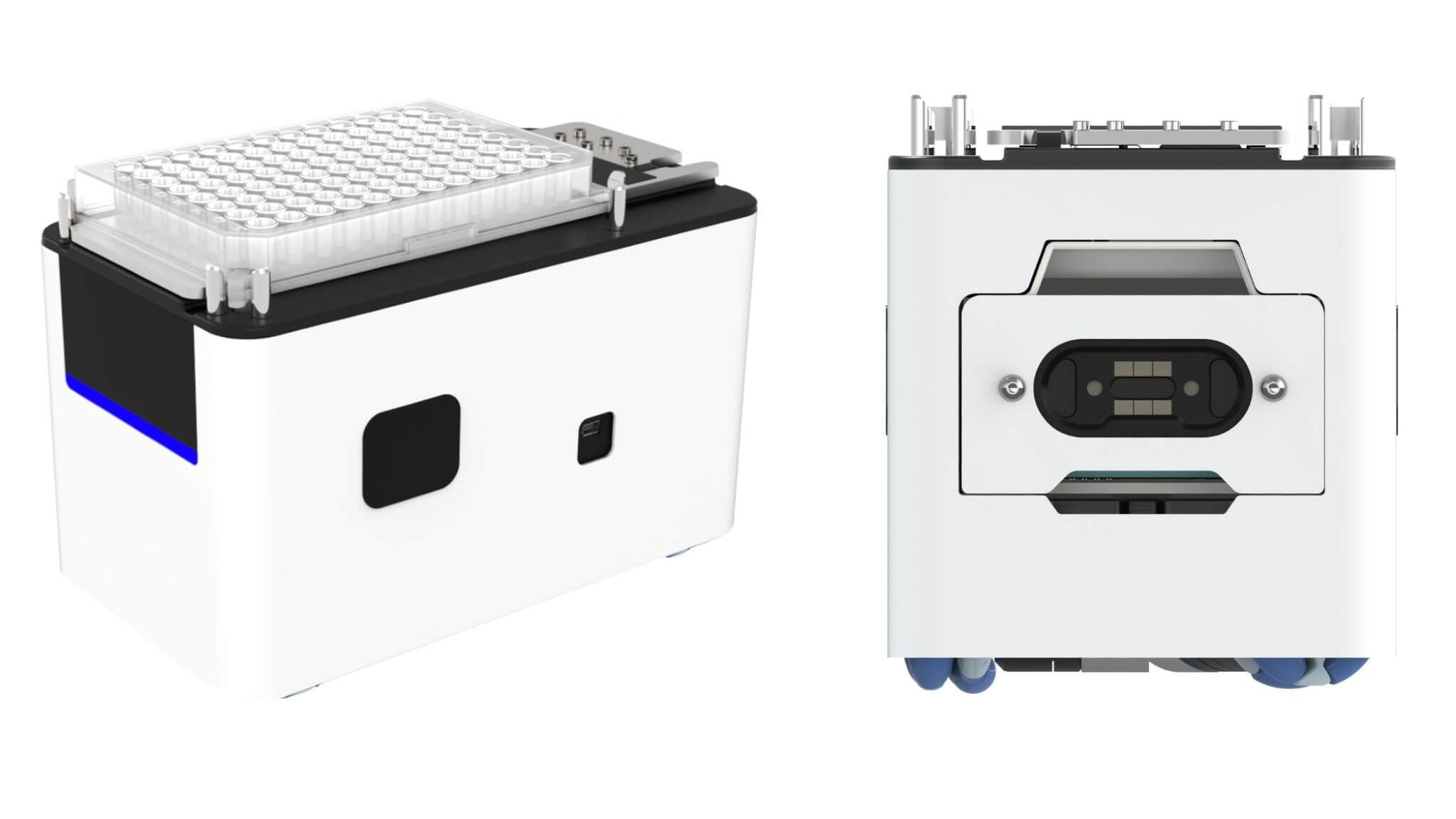
You have mentioned JMP DoE suite. Are your instruments compatible with any other software? Also, can your instruments be integrated with automated work cells?
Essentially, as long as your software can output a .CSV file with concentration or dispense or transfer volume data, we can work with it through our data import wizard. As for integration – absolutely! our liquid handling systems are designed with open APIs, making them seamless to integrate into high-throughput work cells.
What materials are the F.A.S.T. and FLO i8 tips made of?
The FLO i8 tips are crafted from lab grade virgin polypropylene, with their conductive strip being carbon black-impregnated polypropylene. Both these materials are industry standard for pipette tips, known for their inert nature. The F.A.S.T. tips also employ polypropylene for their tip, while the plunger is a made from a special type of plastic used in other positive displacement tip systems, ensuring strength, temperature resilience, and chemical inertness.
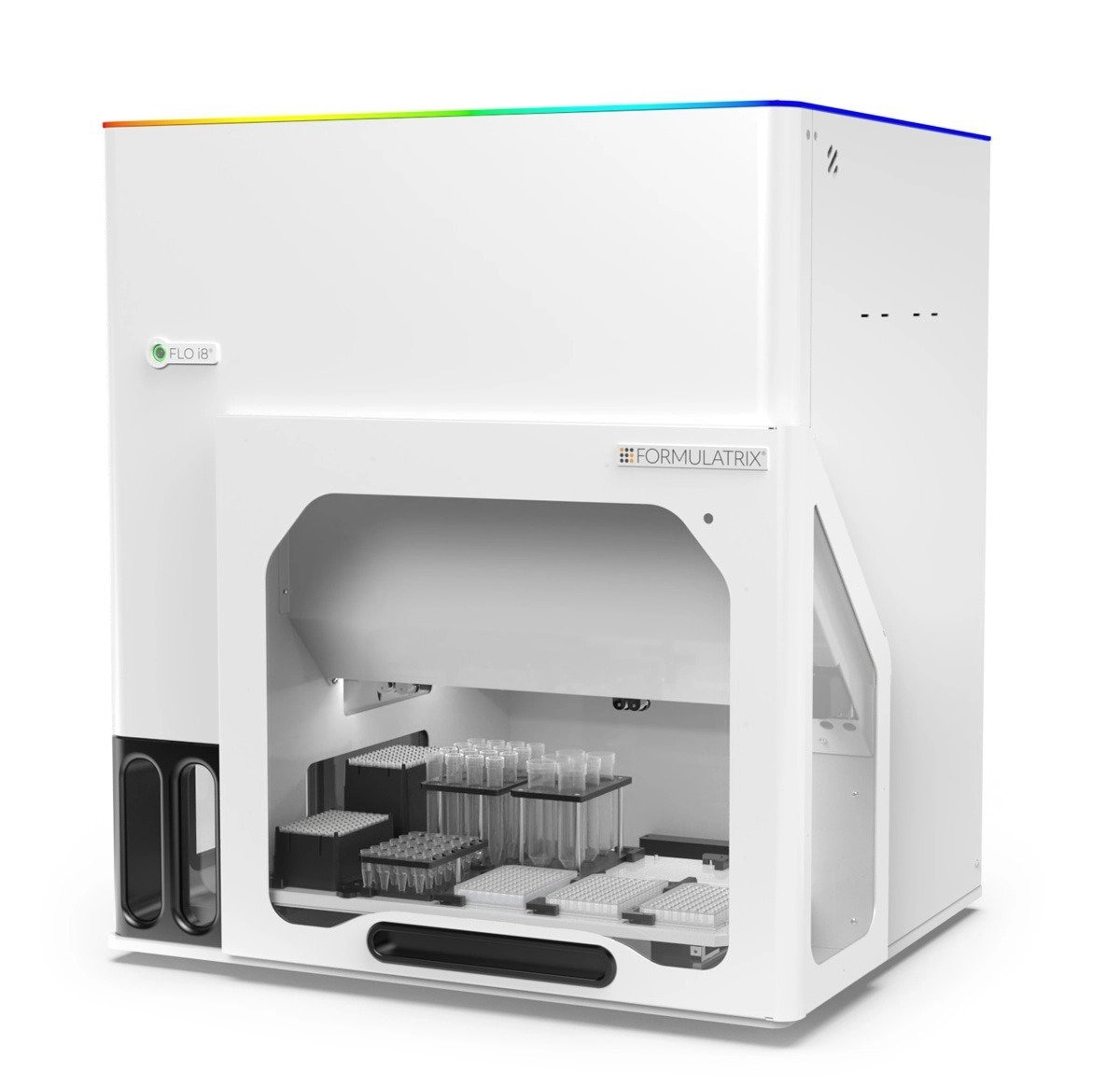
Is the FAST system compatible with the IFC plate from standard Biotools? Can we use the automatic plate definition feature to create an IFC plate definition?
And the answer is Yes!. Because conventional liquid handlers often find IFC plates challenging due to their unique format, people usually interact with them by hand pipetting small volumes manually, which is laborious and can compromise reproducibility.
The F.A.S.T. liquid handler offers the solution to this problem. Its software fully supports all varieties of IFC plate formats and can automate the pipetting operations with high accuracy and precision with its integrated labware teach tool.
In your demonstration, the micro diaphragm technology seemed quite gentle when dispensing organoids. Can you share more about the pressure exerted on these organoids and the maximum particle size the equipment can manage?
That's a good question. When it comes to pressure applied to these diaphragms, Mantis typically operates at 12 to 17 psi, while Tempest is around 13 to 15 psi. The fluid channel diameter of Mantis' LV chip is 250 microns at its narrowest point, whereas for Tempest, it is 380 microns. So, our instrument can easily handle particles smaller than this size without any difficulty.
It appears that positive displacement might be superior to air displacement. Why isn't Flo designed with positive displacement?
That's an interesting point you've raised! Well, it's not always about one being superior to the other. The choice really comes down to the specific application and the flexibility of volume ranges required. Modern science values both technologies, each having its own specialty. For instance, the design decision to use air displacement was to allow maximum precision and accuracy of the system over a wide dynamic range without the need for specific piston or barrel sizes. If you think of the multiple hand pipettors you might use to transfer a half microliter, 10 microliters, and 1000 microliters – we have been able to combine all those pipetting ranges into 1 channel using air displacement, further enhancings the Flo's multi-functionality nature in labs.
In the video where you dispensed three different liquids at the same speed. At the end of the video, I noticed there was a sideways motion, can you explain what that was?
Great observation on that FAST video! That is actually one of the pipetting features of FAST. The system performs a tip touch-off within the well at the end of the dispense operation to ensure that it doesn't carry away any extra liquid droplets.
Next one is about calibrating trays, does the F.A.S.T system require recalibration every time we replace a tray?
Not at all. FAST employs a touch probe to self-calibrate the X, Y, and Z coordinates for each tray slot, and then saves those values. This means you don't need to calibrate the system whenever you replace a tray. Each deck is barcoded, so the calibration is stored per tray, you can have as many trays as you want.
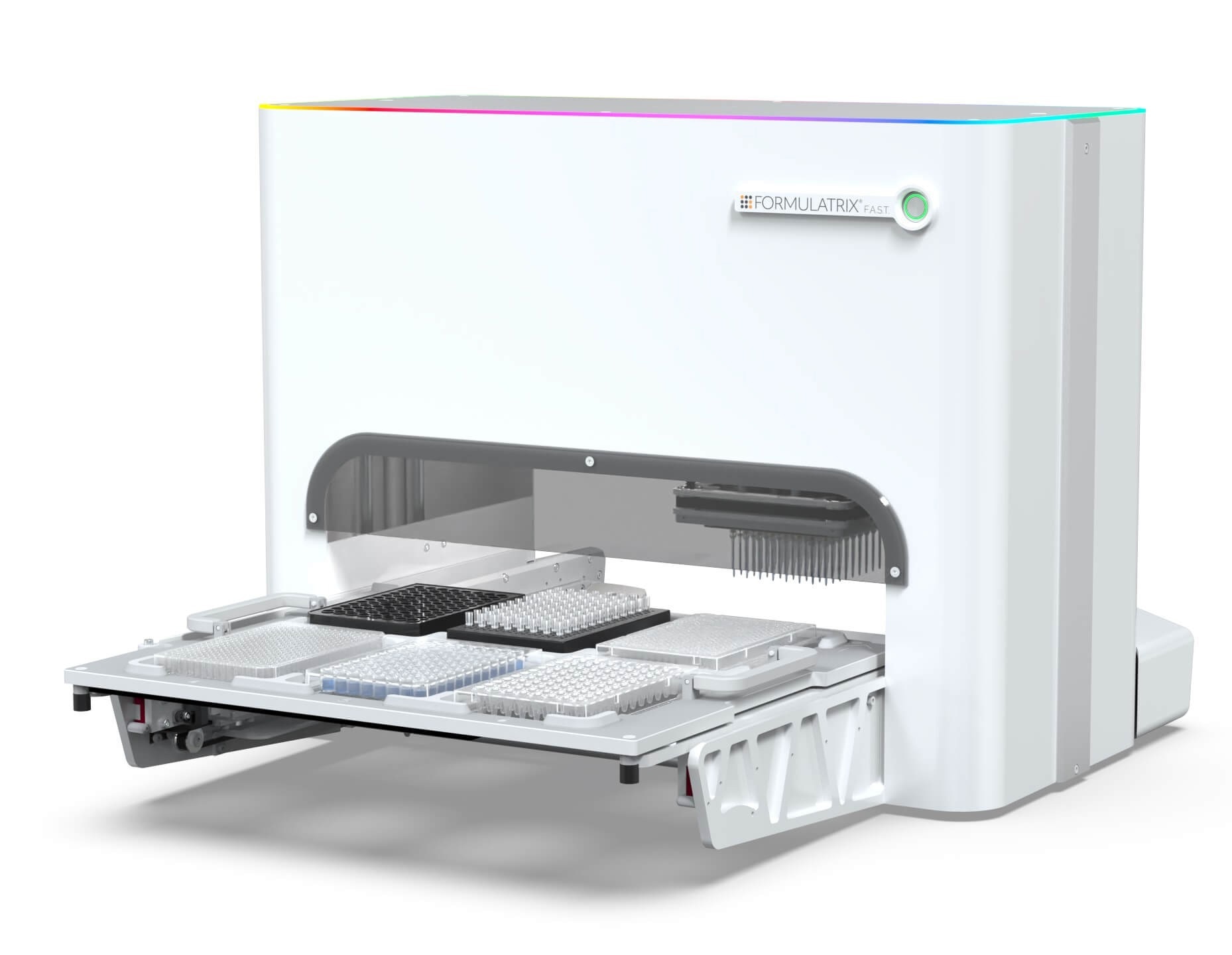
Is the F.A.S.T system appropriate for dispensing cell suspensions or beads?
Absolutely, it can. The tip's design has an orifice that's 0.5 mm at its narrowest point. So essentially, anything smaller than that size can be aspirated and dispensed without any concerns about damage or clogging.
So, how can we ensure the sterilization of the instrument and the chips?
For the Mantis and tempest, our chips features enclosed fluidic channels, which effectively prevent any liquid from entering the instrument itself, keeping it sterile.
The consumable chips are compatible with a wide range of anti-bacterial and cleaning solutions, so you can clean them easily.
You talked about Liquid Sensing; what did you mean by that?
FLO i8 has a flow sensor in each channel that employs pressure-based liquid sensing and conductivity-based liquid level tracking. This feature is particularly handy for organic liquids that aren't conductive. So, this enables it to cater to a broader range of liquids.
About Michael Nilsson
As the Assistant Director of Liquid Handling at FORMULATRIX, Michael applies his passion for engineering and engineering management to the product and project management oversight of the liquid handling and automation product lines, leading 10 product managers and engineers to develop new features and products lines in the portfolio and launch new products in the liquid handling markets.
Michael earned a Ph.D. in Mechanical Engineering from the University of Massachusetts, after completing a Masters and Bachelors in Mechanical Engineering from the same. He began his career as a development engineer at PerkinElmer, where he then gained valuable experience in microfluidic and robotic R&D management as well as operations value engineering project management in a variety of engineering and leadership roles.